Project completion “HochPerForm”
Powerful, compact and now also fast: shape-memory alloy actuators
Many applications, for example in toolmaking and mechanical engineering, require actuators to convert electrical signals into mechanical motion. If the application requires large forces while using minimal installation space, actuators made of thermal shape-memory alloys are the best choice. Their sole drawback lies in their slow cooling process and the resulting low dynamics. Three Fraunhofer institutes joined forces to develop a new class of high load shape-memory actuators that are the first to quickly switch large forces with minimal size and high dynamics.
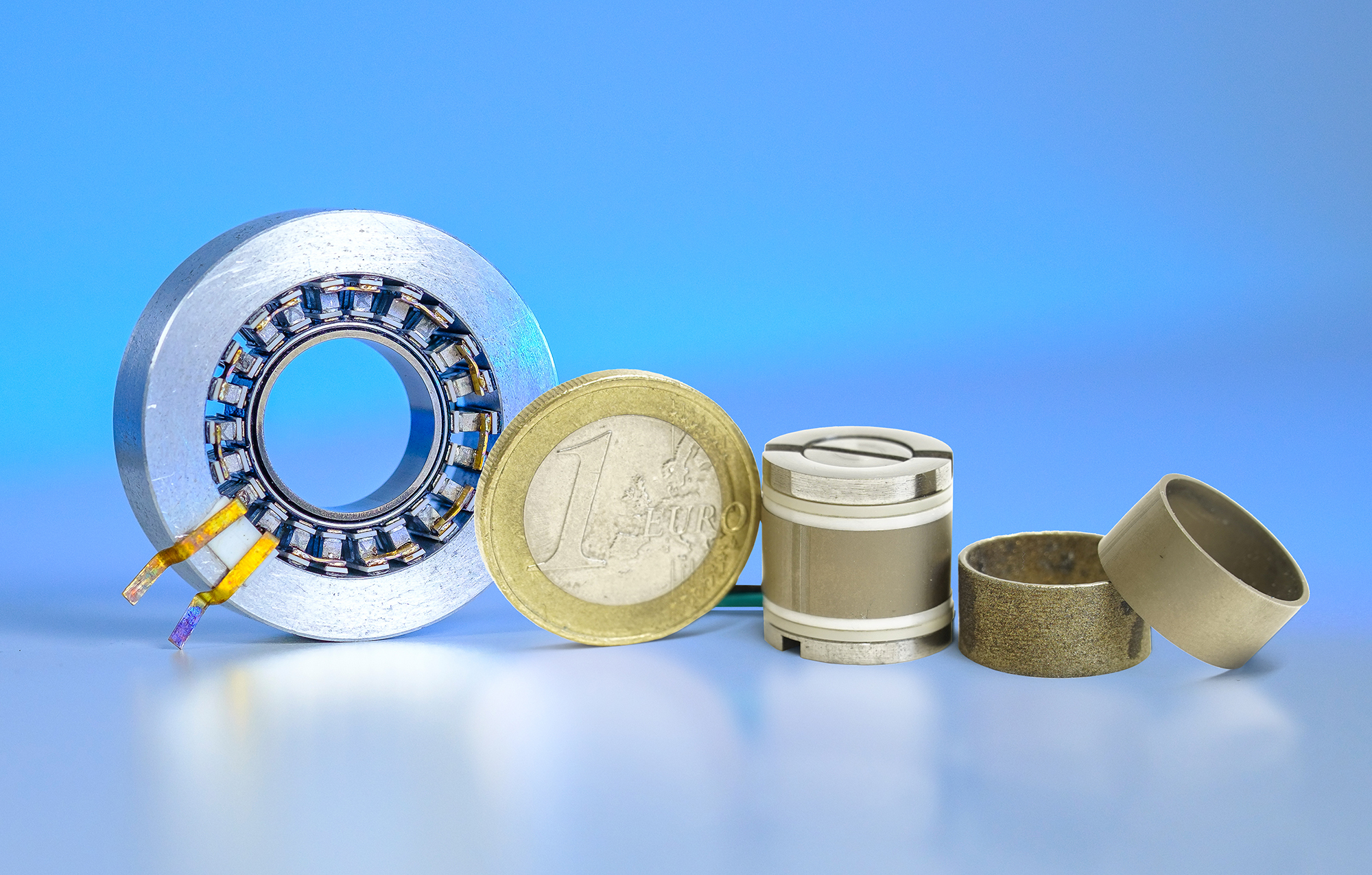
As part of the recently completed HochPerForm research project, a team composed of researchers from Fraunhofer IPM, Fraunhofer IWU and Fraunhofer IFAM has created compact, highly dynamic high load actuators based on thermal shape-memory alloys (SMA). With a diameter of only 15 mm and a length of 16 mm, these novel actuators can lift masses of 500 kg by up to 200 µm. An innovative Peltier temperature control system allows the actuators to switch at frequencies higher than 0.3 Hz. Controlling them requires only two cables connected to a decentralized, cost-effective control electronics unit.
The team started off by developing partial functional models in order to answer the three main questions of the project. One: How can the installation space of the high load SMA actuator be minimized? Two: How can the actuator be brought to the right temperature fast? And three: Can the required SMA components be 3D-printed? Based on their findings, the team developed a high load SMA actuator with much better properties, thanks to its 3D-printed SMA component and powerful temperature control. They used a functional demonstrator to show that the new high load actuators are ideal for tasks such as the fine positioning of production machine components, and are predestined for applications that require large holding and clamping forces.
Innovations in cooling, system design and manufacturing
A team at Fraunhofer IPM used two approaches for rapid cooling of high load SMA actuators: switchable heat pipes and round thermoelectric modules. The second approach, in particular, enabled high dynamic ranges despite the small system size. This opens up completely new applications for SMA actuators in terms of compactness, controllability and simplicity.
The basic high load SMA actuator was developed at Fraunhofer IWU. Besides the SMA component, which functions as an energy converter, it consists of a sophisticated tension and compression rod system. During the development, the Fraunhofer IWU team implemented a modular design that allows high load SMA actuators to be customized.
Up until now, the geometrical freedom and availability of shape-memory components have been a drawback of high load SMA actuators. Fraunhofer IFAM’s team resolved this issue by 3D printing tailored SMA components. With its extensive experience, Fraunhofer IFAM was also able to significantly improve the functional characteristics such as hysteresis and degradation through laser powder bed fusion (L-PBF).
Project “HochPerForm”
The project HochPerForm (Hochkompakte, schnelle Aktorik auf Basis von Formgedächtnislegierungen - Highly compact, fast actuators based on shape memory alloys) was funded by the Fraunhofer-Gesellschaft as part of the PREPARE program. Duration: 01.03.2020 – 31.12.2023 Project partners:
|